News & Articles
Putting the K Back in Copper
December 23rd, 2016
by Aaron Fruit
Fixing a Leaking Chimney, Replacing a Cedar Roof
The Problem:
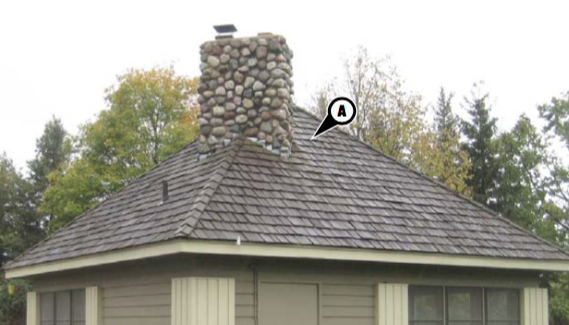
This is the community building owned by an exclusive neighborhood association in Orono. For years different roofers were hired to address the leaking chimney (A), only to ultimately fail in their attempts. Their answer, caulk and tar (B). Here is the pesky leak as seen from the mechanical room of the building (C).
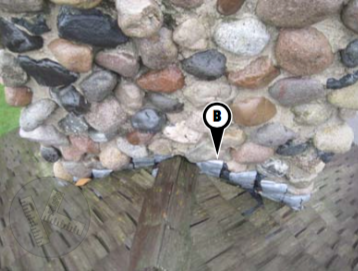
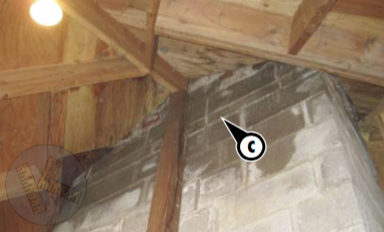
The Solution:
We installed a new 24” medium hand-split cedar shake roof (D) and a custom copper box riglet flashing (E) around the perimeter of the chimney. This required a deep kerf cut into the field stone and a few little adjustments to the roof decking around the chimney. Our roofing crew established the smallest box riglet dimensions by drawing plumb lines down from the maximum overhang of each field stone on each side of the chimney. The step tins were installed along those lines as each course of new cedar shakes was installed. Finally, we returned to saw in the top half of the box riglet.
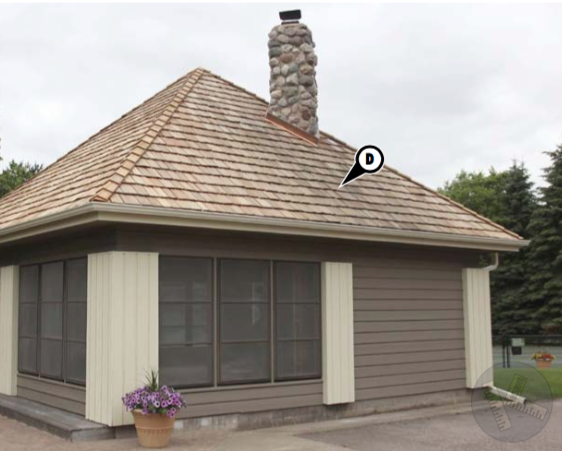
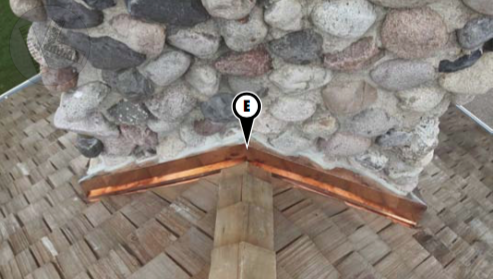
Posted in Uncategorized
Creativity Matters
December 9th, 2016
by Aaron Fruit
Remodeling a Bumpout Window With a Bad Leak in Minnetonka
The Problem:
Imagine you have a window bumpout like the one here (below). The builder was running a little thin on his margin so he skimped on a few details. Now 13 years later, you have rotten siding, soggy millwork, and a roof that leaks. Now imagine that for the first time you looked at this feature on the front of your beautiful home and realized not only that it was rotten, but it was ugly too. You could find a roofer to fix the metal roof and then a carpenter to rebuild the bumpout. Or, you could call Kuhl to do it all and redesign a few key elements in the process to add a little more class to your home.
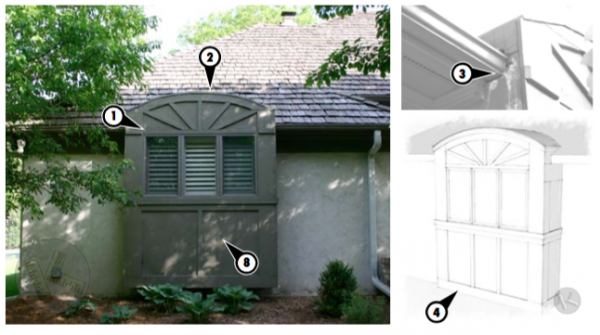
Things That Make Us Cringe Upon Inspection:
- Missing z-flashing above window.
- Thin gauge steel roof, rusted through and poorly installed.
- Gutters terminated too close to wood resulting in big time rotting.
- The overall design felt utilitarian and ‘builder-grade’.
- Rotten 1×2’s arranged in a quasi-sunburst pattern.
- Steel roof installed short from facia (= more rotting issues).
- No kickout flashing (code required, and smart besides.)
- Totally rotten panels. And, how hard would it have been to add one more vertical stile to carry the lines of the window mullions through visually? Answer, not hard. It just requires some design experience.
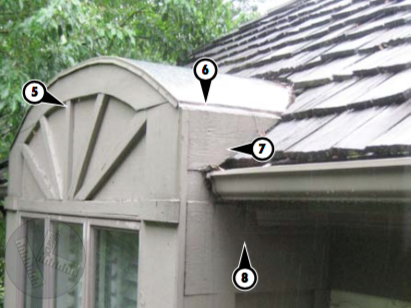
Posted in Uncategorized
?@%&#! Storm Chasers!
December 4th, 2016
by Aaron Fruit
One Edina Man’s Story of Dealing with Storm Chasers and His Cedar Shake Roof
The Problem:
Jerry’s roof was replaced by some storm chasers after a hail storm in 2006. His insurance company agreed to replace the skylight units (1) but refused to pay for the replacement of the curbs and curb flashing (2) because “they were not dented by the hail”. So poor Jerry had new skylights installed on top of old, crusty curbs. It wasn’t long before they started leaking. He chased the insurance company and the roofing company, who both successfully pointed the finger at the other. Sorry Jerry. You lose.
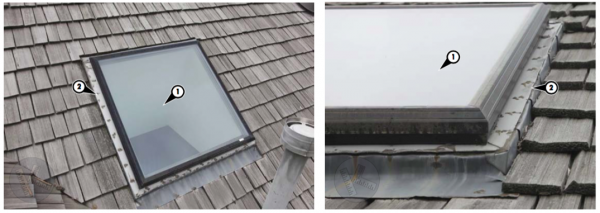
The Solution:
There are two parts to this solution. First, before agreeing to any settlement with his insurance company, Jerry should have called Kuhl to sniff around and examine the claim. We would not have allowed them deny the curb replacements. Period. We have some experienced former adjusters on staff who know all of the games insurance companies play. They don’t miss a thing.
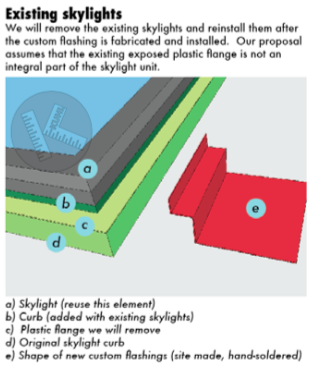
Would have, should have, could have. The fact was that Jerry was left holding the bag and someone had to fix these skylights. That’s when he called us. We removed the skylights and bad curb flashings then fabricated a custom copper flashing to accommodate the existing roof flashing and the existing non-standard curbs. After we fabbed up the flashings it was a simple matter of soldering it all together and repairing the roof around each unit.
Now years later, there have been no leaks.
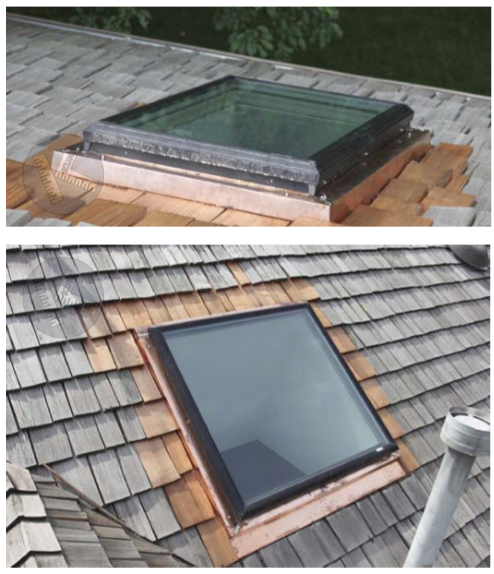
Posted in Uncategorized
Good From Afar (But Far From Good)
November 25th, 2016
by Aaron Fruit
Cedar Roof Cleaning Franchise Perpetrates Another Bad Roof Renew Job in Orono
The Problem:
We lose a hand-full of cedar roof restoration jobs each season to a competitor that likes to include “50 or so” shake replacements in their bid, regardless of the roofs age or condition. It’s extra frustrating when we are called back to inspect the work they did because it ‘feels incomplete’ to the homeowner. Almost without exception we find unaddressed issues with this company’s work. Here is one roof in Orono we inspected in August of 2011 that had just been ‘renewed’ by another company. It was still drying out from the washing when we arrived the next day. We won’t mention names, but it was a company that specializes in washing roofs and does a lot of advertising to fill their schedule. Clearly they don’t specialize in repairs. Oh snap!
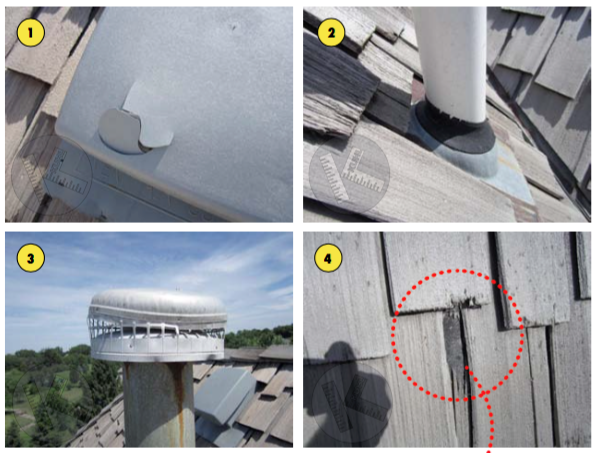
- Cracked passive roof vent – needs replacement.
- Damaged boot flashing – needs to be replaced.
- Crushed Type-B flue cap – serious issue and potentially dangerous – may cause carbon monoxide to reach toxic levels in the home.
- Open keyway between two shakes – this is an example of a shake that should have been replaced during the roof renewing process.
Here’s the skinny on cedar roof repairs. If you want to limit what you spend, make sure the person doing the repairs addresses the most severe areas first. You should have an understanding after the repairs have been performed as to what work was left undone, if any. This client needed another $1,512 in repairs to complete the job.
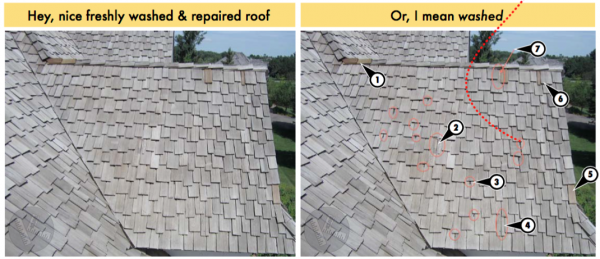
List of Issues Left Unaddressed After Repairs Were Completed:
- No problems here. The ridge pieces were installed properly.
- Missing shake – needs a replacement.
- Open keyway – 1 of 11 such oversights on this roof area alone.
- Crack in the shake aligns with keyway in the course above.
- Shake installed upside down.
- Code requires minimum shake of 2″. This doesn’t meet code.
- Maximum keyway spacing allowed by code has been exceeded.
Posted in Uncategorized
Ugly Chimneys in Eden Prairie
November 11th, 2016
by Aaron Fruit
Clients Chimneys Were Leaking, But at Least They Were Super Ugly
The Problem:
Our Eden Prairie homeowner needed a new cedar shake roof and two chimneys rebuilt. More than a simple chimney rebuild, these babies needed a redesign (thank you 1970’s). The 12” thick lump of concrete originally installed on top just wasn’t going to cut it anymore (A). Yes, they were not good looking, but worse, they allowed water to soak into the stone and into the home because there was not an adequate ‘drip’ (B), which is an overhang to encourage water to miss the walls of the chimney. Replacing the concrete washcaps alone would not have addressed the utilitarian character of these chimneys either. They needed some design (C) help and a team of craftsmen to pull it all together. Enter Kuhl.
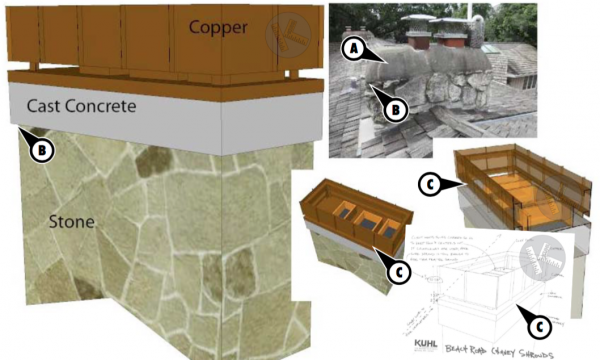
The Solution:
After forming and pouring the new chimney caps (D) we designed and installed the copper chimney shrouds (E). Each chimney shroud accommodates the exact dimensions of the cap beneath as well as the different flue penetrations. We wrapped the copper up and into each clay flue to keep water out of the system completely (F). The resulting chimney treatments look phenomenal from the curb and will keep the home free of leaks for years to come.
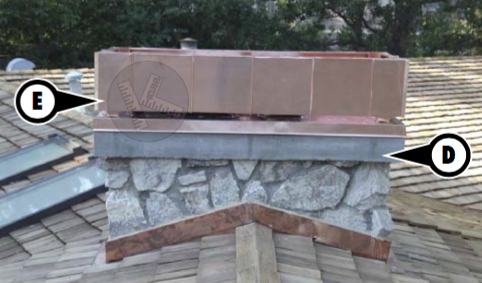
Posted in Uncategorized
Roofing + Design + Carpentry = Happy Client
October 28th, 2016
by Aaron Fruit
Roofing Contractor Uses Designers and Carpenters to Help Wayzata Commercial Roofing Client
The Problem:
We had worked on Craig’s residence a few times over the past fifteen years. He invited us to give him a bid on one of his commercial properties. It had a tired cedar shingle roof with dated treatments around each window. He wanted to make the building feel ‘more commercially’ and less pseudo 70’s Colonial. For us it was a simple project involving a few of our guys. He hired us to avoid the design and management headaches of trying to do all of the coordination himself.
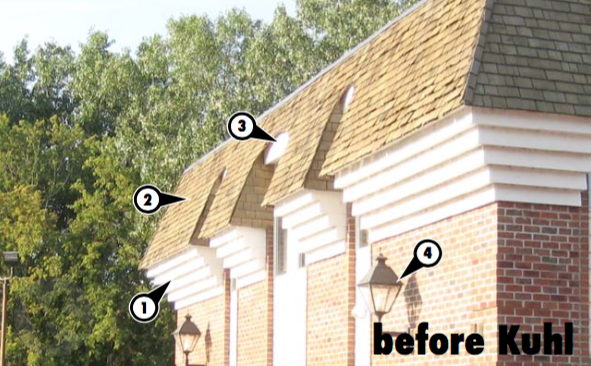
Things to fix:
- Dirty white paint on stepped soffits.
- 24 yearly cedar shingle roof.
- Dated ‘eyebrow’ around each window.
- Giant, antiquated light fixtures.
The Plan:
Our designers devised a relative simple and cost effective solution using Hardie panel, plywood and some basic framing. To make sure it was exactly what Craig wanted, we drew it up in detail for his review. We do that frequently.
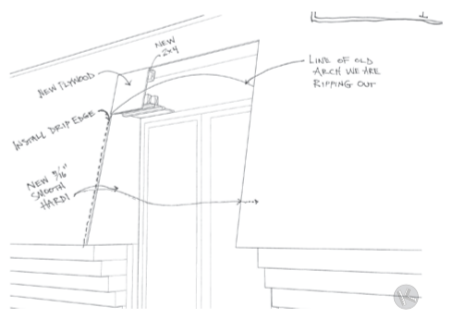
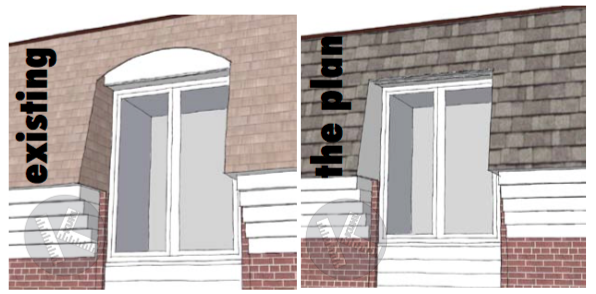
The Result:
There isn’t another roofing or siding company in the Twin Cities that can match our capabilities from design to specifications to execution.
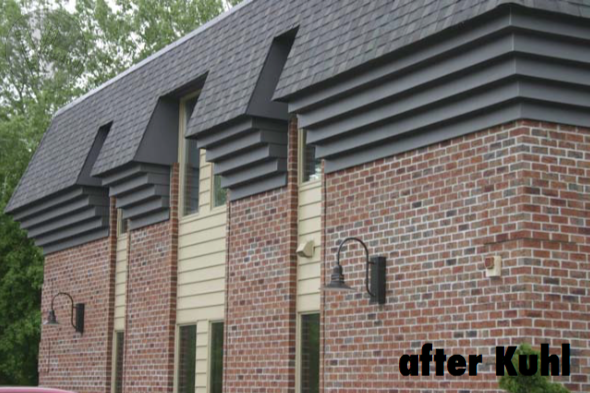
Our team quickly assembled the plan to:
- Repair, prime and paint the soffits.
- Replace the roof with heavy asphalt shingles.
- Rebuild the window surrounds.
- Replace the light fixtures.
- Specify all materials and colors.
- Design and manage the whole thing.
Posted in Uncategorized
Oh, The Difference a Door Makes
October 14th, 2016
by Aaron Fruit
Amazing Deephaven Home with Ugly Front Door Gets a Custom Door from Contractor
The Problem: You have a really nice home with a really crappy front door. That’s no way to welcome your guests.
The History: We first met Cindy in 1998, when we washed, repaired, and preserved her cedar shake roof in Deephaven. We’ve continued to work for her until today, doing a variety of projects including installing a new cedar roof, copper gutters, custom cabinetry, painting and masonry. Cindy is the embodiment of what we look to have with everyone we meet. When her new cedar roof needs cleaning and sealing years from now we will be right there.
The Plan: Our client, Cindy, approached us about making a custom black walnut front door because nothing in a catalog was going to cut it. We came up with 5 designs that were appropriate for the style of her home. We ended building a hybrid of a few of them. The finished door was 42” wide and weighed almost 175 pounds. In addition to the bad door with no glass for natural light, the existing door frame needed meticulous restoration, like paint stripper and toothpicks restoration. We removed the door frame and restored it in our shop before reinstalling.
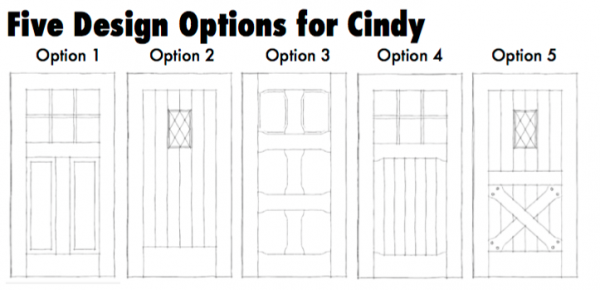
The Result:
Door specifications: 2.5” thick black American walnut, double beveled insulated true divided lights, mortise and tenon construction with locking dowels. Worm holed, distressed finish. Rocky Mountain Hardware handle set.
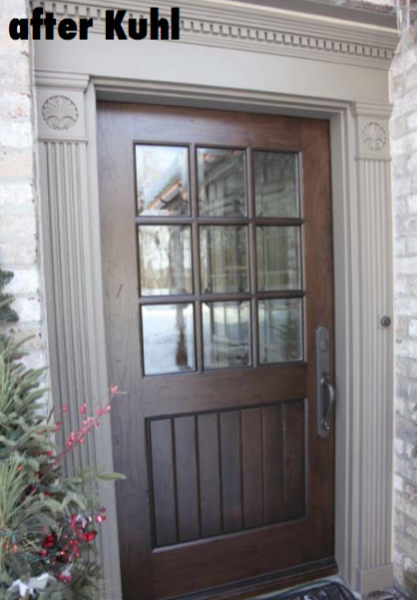
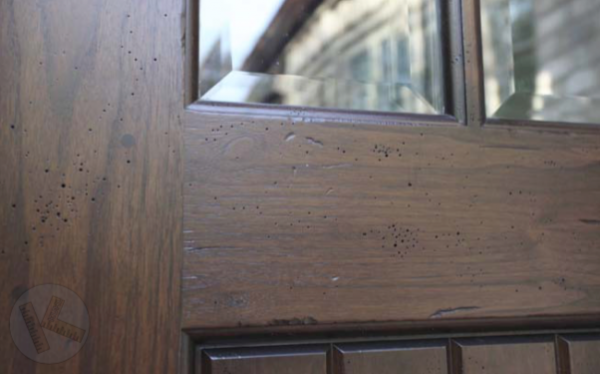
Posted in Uncategorized
Upgrading a Chimney
October 7th, 2016
by Aaron Fruit
Repair Your Chimney or Enhance the Look of Your Exterior
The Problem
Your chimney is failing, it looks like this, and someone wants $3,200 to fix it. Ouch.
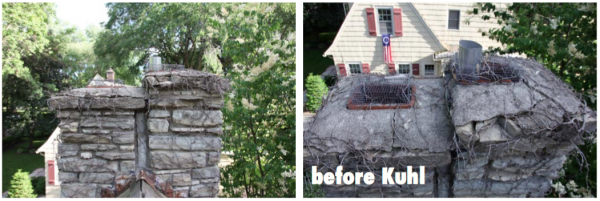
The Solution
Hire someone with experienced designers on staff who know the difference between concepts like Cotswold and Tudor. It would have been easy enough to simply fix this chimney; we do that all the time. But we really like making homes look better so we floated the idea of some glazed chimney pots. It turns out that our estimate for all of the work was $107.00 higher than the other bid our clients received. And their proposal didn’t include killer chimney pots.
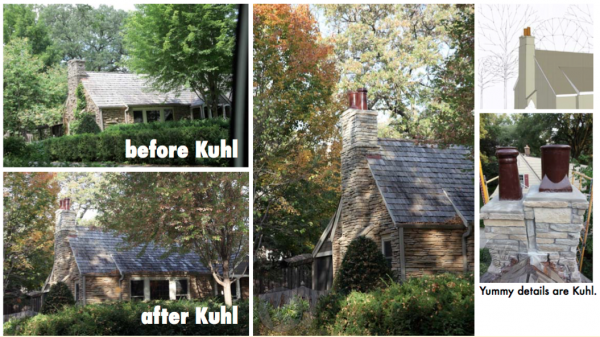
Posted in Uncategorized
Slouching tree, Hidden Challenge
September 7th, 2016
by Aaron Fruit
Creative Remodeling Contractor Finds Solution to Odd Problem
The Problem:
A cedar roof restoration client of ours had an old oak tree that added tremendous character to her property. The problem was that over years the heavy limb (right) sank lower and lower and our client kept buying higher and higher vehicles. She couldn’t stand the idea of chopping the limb off, (or of driving a Ford Fiesta) so it was time to build a limb crutch. We theorized that whatever we built needed to be somewhat dynamic in that it needed to allow for the movement of the tree in the wind.
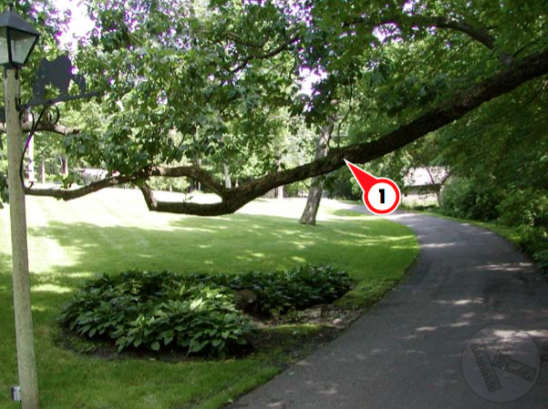
(1) Car whacking point
Our clients have learned that we shy away from nothing when it comes to solving problems. So she called.
The Solution:
We tracked down some hand hewn timbers from a log supplier near Ely, Minnesota. The shipping unfortunately cost more than the logs so we paid one of our guys for a little road trip. When he brought the goods back to the workshop we realized that they were a bit massive for conventional tools. We notched them out with a chain saw, roped and bolted them together and presto! We had made the first and most likely last tree crutch of our careers. We calculated that the limb weighed somewhere between 1500 and 2000 lbs so it had to be strong. Another challenge was that we couldn’t nail or screw the crutch to the tree because that wouldn’t allow for natural movement through the seasons. After we were done we achieved a 10 foot clearance under the lowest point on the branch. Seven years later the tree and the client are still peacefully coexisting. Got a problem? Just Kuhl it.
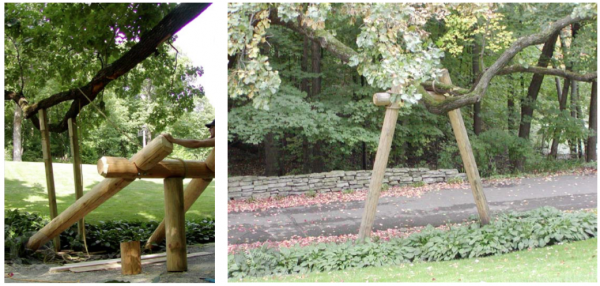
Posted in Uncategorized
Keeping Squirrels Out of Your Roof
September 2nd, 2016
by Aaron Fruit
Animal Damage to Roofs in the Minneapolis Area
The Problem:
Red Squirrel
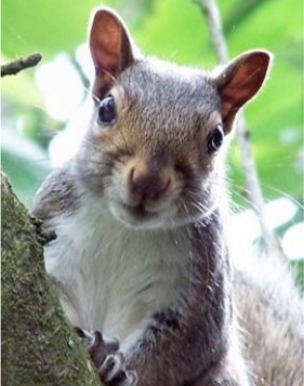
Scientific Name – Sciurus Vulgaris
Unscientific Name – Bastardus Rodentae
Size – Body length of about 4 inchs (not including tail)
Diet – Nuts, acorns, seeds, and your cedar roof
Preferred habitat – Mainly a tree dweller, occasionally a roof dweller
This guy popped out from inside the roof vent when Steve was inspecting a wood roof in Shorewood, Minnesota. Squirrels frequently chew into wood roofs causing damage ranging from minor cosmetics to major leaks and house fires. In fact, fire inspectors estimate that each year in the United States over 12,000 house fires are caused by squirrels chewing into wires – Nuts! Whether it’s a roof leak or a potential fire, it’s safe to say that keeping squirrels out of your attic is a good idea.
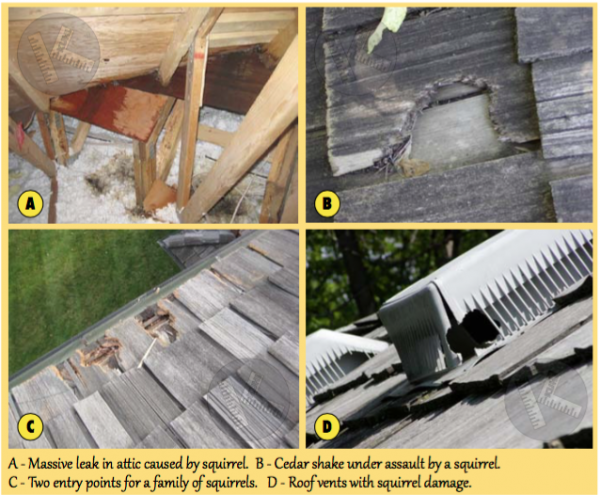
Still not convinced it’s wise to keep squirrels out of your attic? Here are a few other reasons:
- Their holes provide access to other critters like bats, birds, mice and bees.
- When-not if-they breed your problems are multiplied by 4 or 5 times.
- Squirrels bring fleas, ticks, and mites into your house, which can spread to your living areas.
- Aside from fires, they can cause real property damage to anything they come across.
- Rodent infestations can cause home sellers a real headache when putting their homes up for sale.
- Although rare, squirrels can and do infect people with rabies.
The Solution:
Sorry folks. There is no known way to squirrel-proof the average American home. We suggest a few common sense approaches to minimizing the likelihood that your home will attract squirrels:
- Keep trees trimmed back from your home a minimum of five to ten feet.
- Sadly, stop feeding birds and other wildlife, as that same food attracts squirrels.
- Address new entrances as soon as you notice them. Don’t wait for your home to become familiar.
- Treat areas on your home with commercial squirrel repellants (available online).
Posted in Uncategorized